Basic theories of dust cleaning-method and mechanism of air reverse dust cleaning
Method and mechanism of air reverse dust cleaning
Air reverse blow dust cleaning is a kind of dust cleaning method which uses the opposite air flow to make the filter bag deform and cause the dust layer to fall off. In addition to the deformation of the filter bag, the air velocity of the air reverse blowing is also an important reason for the dust layer falling off.
The air flow of ash cleaning by this way can be provided by the main fan of the system or by a separate fan. According to the pressure condition of the ash cleaning air flow in the filter bag, if positive pressure mode is adopted, it is called positive pressure air reverse blowing ash cleaning; if negative pressure mode is adopted, it becomes negative pressure air reverse blowing ash cleaning.
The air reverse blow ash cleaning mostly adopts the chamber work system, and uses the valve to adjust automatically to generate the reverse air flow room by room.
On the one hand, the reverse air flow directly impacts the dust block; on the other hand, due to the change of air flow direction, the filter bag produces expansion and contraction deformation, which makes the dust block fall off. The size of the reversed blowing air directly affects the cleaning effect.
The process of air reversed blow dust cleaning is shown in Figure 1.
The air distribution on the whole filter bag is uniform. The vibration is not violent, so the damage of the filter bag is small. The long filter bag (4-12m) is usually used for air reversed blow dust cleaning, and the steady filtering wind speed of ash cleaning intensity is generally 0.6-1.2m/min, and all of them are cleaned during stopping the wind.
High pressure air flow is used for air reversed blowing, for example, rotary reversed blowing bag type dust remover can get better cleaning effect under the working condition of filtration, but medium pressure or high pressure fan shall be set additionally. In this way, high filtering wind speed is adopted.
For dust cleaning by reverse blowing, the falling resistance of dust layer without compaction is not large. For a dust layer with a median diameter of 1 μ m and a density of 6 * 10 ^ 3 kg / m3, its resistance is only 50Pa. However, the air pressure does not act on the whole area of the dust layer, but on the opening. Therefore, in order to make the dust fall off, it is necessary to apply a higher reversed wind force on the filter cloth. The higher the porosity of the filter material is, the lower the residual pressure is required for the dust layer to break away, and the higher the resistance of ash removal is. For each kind of filter cloth, there is a maximum flow rate of air reversed blow ash cleaning. Exceeding this value does not significantly increase the dust separation, but only causes excessive energy consumption. It is enough to reach 0.033m/s (i.e. about 2m / min) for the reversed air velocity of the filter cloth pore. The flexible filter cloth always deforms in the process of counter blowing, which will cause the movement of dust accumulation layer and encourage it to fall off. Therefore, the pressure difference consumed in reversed blowing is not high. If the median diameter of the dust collected in the filter bag is 3-15 μ m, the pressure difference is 500-1000pa. During reverse blowing, due to deformation, the filter bag shrinks and folds appear on the filter bag, with its diameter reduced (see Fig. 2).
In the process of reverse blowing, the shrinkage of the filter bag should not lead to a large reduction of the diameter of the filter bag and large folds, so as to avoid affecting the flow of the blown gas and the normal stripping of dust. For this reason, the filter bags are equipped with horizontal push support rings to increase the tension of the filter bags and limit the pressure of the jet air flow. The support ring is not arranged according to the average distance along the length of the filter bag, but is arranged and positioned from the top of the filter bag according to the 5-6 times the diameter of filter bags in the upper part, and is separated from each other; the distance to the bottom of the filter bag is shortened to 2-3 times the diameter of the filter bag. This arrangement is to ensure that the reverse air flow used for ash cleaning can flow freely when the ash is cleaned by reverse blowing. For example, for a long filter bag with a diameter of 296mm (the length of the filter bag is generally 10m), the distance distribution of the support ring is (1800 ± 10) mm, (1500 ± 10) mm, (1200 ± 10) mm, (900 ± 10) mm, (700 ± 10) mm, etc. from the top to the bottom.
In order to limit the pressure difference between the inside and outside of the filter bag, the diameter of the injection valve is usually smaller than that of the exhaust pipe. Sometimes the dust remover is equipped with a damper valve to ensure the best pressure drop on the filter bag during the ash cleaning process.
If the peeling off of dust is not uniform in the process of reverse air blowing, the dust will first fall off in the local place with large deformation of filter bag and coarse particle size of accumulated dust, and the main mass of blowing gas will immediately multiply and concentrate here, while the dust layer in other places is still stored. Therefore, this kind of dust removal is not effective. Only the good dust removal on all filter bags can be effective.
From the dispersion and quality of dust, the distribution of dust along the height of the filter bag is uneven. The coarsest components are deposited in the lower and middle parts of the filter bag, while the thinnest and hard to separate components are deposited in the upper part (see Figure 3).
The results show that the efficiency of purification at the beginning of filtration period depends on the degree of ash removal. When the resistance after cleaning is reduced to 270-230pa, the dust concentration from the filter bag layer in the first 3 minutes is as much as 7 times as that before cleaning; after that, the penetration of dust is gradually reduced (as shown in Figure 4). This test is to use quartz dust with a median diameter of 8 microns to test polyester filter cloth.
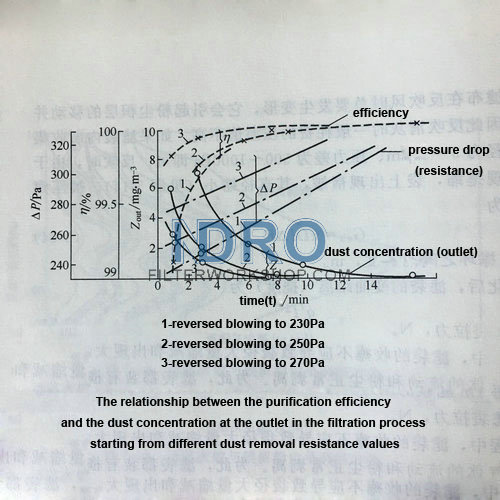
The duration of blowback depends on the length of filter bag and dust settling time. For 8-10m long filter bag, there should be 20-25s, while for smaller length filter bag, it can be reduced to 10-15s (see Figure 5). Long time back blowing will not settle the remaining resistance, but will only increase energy consumption and dust penetration rate.
In some cases, in order to improve the separation effect of the fine dust part and reduce the air consumption of back blowing, the back blowing process is arranged as intermittent type, with 1-2 interruptions in the middle, each section of back blowing lasts for 4-6s. Due to the supplementary deformation of the filter cloth, the dust falling off can be improved to some extent. Fig. 6 below shows the resistance due to the number of air reversed blowing. When the number of reversed blowing is more than 2 times, the influence on the drop of resistance will be weakened gradually. Therefore, only one or two discontinuities can be designed.
A Metallurgical Construction Research Institute has carried out an experimental study on the residual resistance of the bag type dust remover by using the test equipment in Figure 7. The filter cloth used in the test is different glass fiber filter cloth, and the test dust is talcum powder and silica powder. The so-called residual resistance refers to the residual pressure difference of filter cloth after dust removal. Residual resistance is caused by dust particles, which are attached to the filter cloth fiber to be removed. The test results are as follows:
1) The effect of load on residual resistance. The relationship between different loads and residual resistance is shown in Figure 8. Under the same final resistance, no matter what filter cloth and dust are used, the residual resistance always increases with the increase of filtration speed. When the filtration speed increases, the positive pressure on the dust layer increases, and the corresponding dust layer becomes more dense. The binding force between dust particles and the adhesion between dust and fiber are enhanced, so the residual resistance increases.
2) Influence of dust type on residual resistance. It can be seen from Fig. 9 that the residual resistance of filtered silica powder is greater than that of talc powder under the same reverse blowing speed under the same other conditions. One of the reasons is that silica powder has high water absorption, and the adhesion between dust particles and between dust and fiber is higher than that of talc powder.
3) The influence of fabric structure on the residual resistance. As can be seen from Fig. 10, due to the different textile structure of the filter cloth, the reverse blowing effect is also different. The residual resistance of single-sided velvet cotton filter cloth is the largest, and that of 0.19mm thick satin glass fiber filter cloth is the smallest. When the air reversed blowing speed is 2m / min, the residual resistance of the former is 260pa higher than that of the latter. In the same weaving method (satin), the effect of reverse blowing is related to the thickness of the filter cloth, the existence of fluff on the surface of the filter cloth, the structure of the filter cloth and the physical properties of the filter cloth.
4) The influence of reversed blowing speed and times on the residual resistance. Under the same conditions, because of the different air reversed blowing speed, there are obvious differences in the ash removal effect. With the decrease of the counter blowing speed, the residual resistance increases correspondingly. With the change of filtering speed, the relationship is different. Taking Figure 8(a) as an example, the absolute difference of the residual resistance of the blowback speed of 1.3m/min, 0.5m/min and 2.0m/min is 360pa, while the difference is only 120pa when the filtration speed drops to 0.67m/min. Obviously, when the filtration speed is reduced and the positive pressure on the dust layer is also reduced, the porosity of the dust layer is also large, and the adhesion between particles is reduced, so the influence of the counter blowing speed is not significant.
5) The main factors that affect the dust cleaning effect are the air velocity, the deformation degree of the filter bag and the shaking caused by the collision between the filter bag and the frame. The last two factors are also the result of the air flow.